Discrete Geometric Space
Embodied Scale Kinetic Facade Art Installation | 2023 | Hangzhou, Zhejiang
This work attempts to use spatial installations as a medium to contemplate the relationship between the real world and the virtual world in an embodied manner. On the surface, the metaverse appears decentralized, but at its core, it may be highly centralized. For individuals, closed systems can create a perception of a fictional self, while openness allows for a connection to the real world.
In terms of geometric form, stability in the two-dimensional direction is achieved through the incorporation of regularly embedded graphics and hinge points. The motion mechanism utilizes a single power source to drive 484 panels on four faces. In terms of sensing and control, an Arduino embedded platform, along with sensors, lighting, and music, establishes a feedback mechanism for the expandable skin, providing an embodied spatial experience.
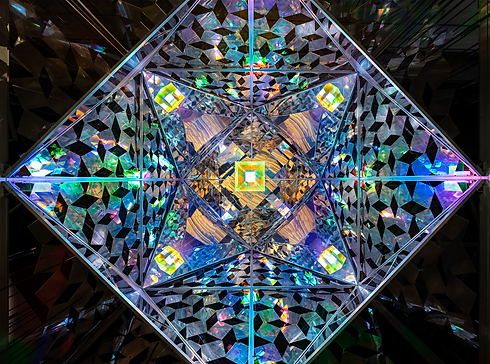

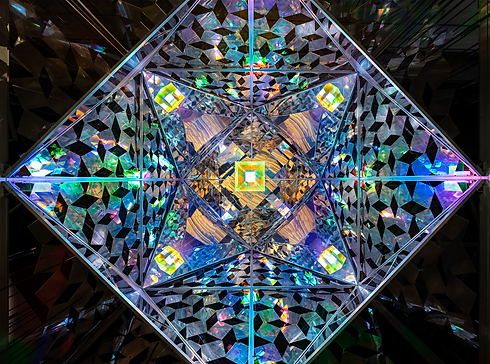

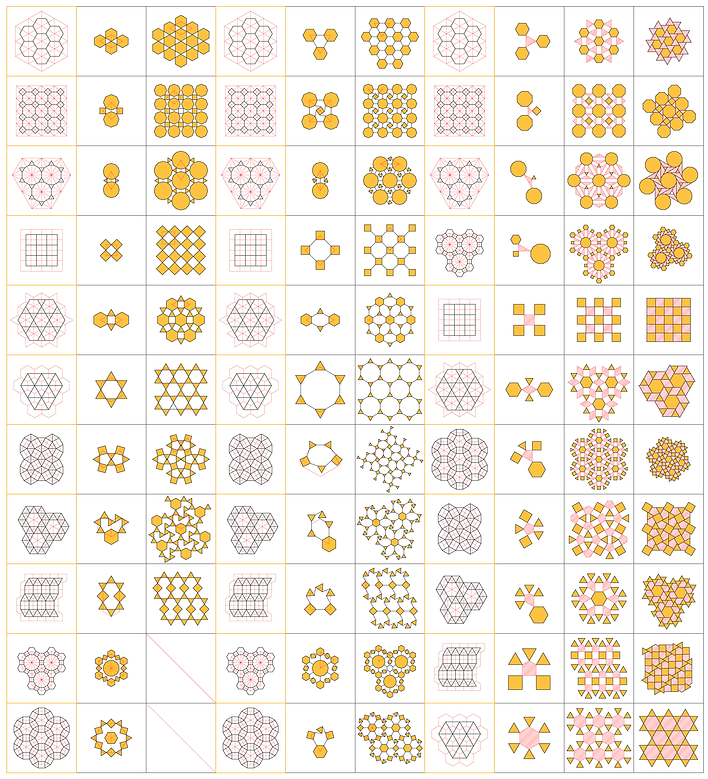
Starting from the topological transformations of embedding, an analysis of dynamic embedding is conducted. Subsequently, based on the principle of duality, the generation methods for the geometric form of dynamic architectural skins are categorized into three types: embedding prototype; embedding prototype with added edges; and embedding prototype with added faces. The study focuses on exploring the relationship between each category and dual embedding, outlining the generation operations.Through this research, a systematic and versatile method for generating dynamic geometric skin forms has been obtained.
In this approach, the object selection is uniform embedding, and dynamic unit geometric transformations are generated through the relationship with dual embedding. This method does not introduce new component types, and the closed state of the dynamic unit is the original embedding type, with two out of the 11 uniform embeddings unable to undergo such transformations. Subsequently, the study investigates the generative methods for dynamic embedding with added edges and faces. Similarly, by exploring the relationship with dual embedding for dynamic unit geometric transformations, this method introduces edges or faces as new components, and all 11 uniform embeddings can undergo such transformations.
The responsive circuit consists of sensors, an Arduino circuit board, a driver, LED device lights, and a motor. Eight active diffuse reflection infrared sensors are used as sensors, installed on the frame above the bottom of the outer frame. Each sensor has an approximate sensing distance of 4m and a sensing range of a 30-40° cone angle. The driver employs an intelligent motor drive module with good driving and braking effects. A 24V permanent magnet DC reduction motor is chosen for the motor, capable of overcoming friction and the weight of the panels during the process of driving the steel cables.


Each side of the device is composed of eleven panels both vertically and horizontally. Leveraging the central nature of the two-dimensional unfolding, a cross frame is added at the center of each facade to introduce a fixed point. This central point serves as a pivot for the force, reducing the overall length of the suspended unit to 1/4 to prevent conflicts with the internal fixed structure in case of inward deformation of the facade.
The installation utilizes hinged points. All units are expanded one full rotation based on geometric shapes and divided into four layers, with inter-layer hinges between each pair. Nodes with volume would conflict geometrically when the facade is closed. To avoid collisions between nodes and excessive construction thickness, all hinge points are rotated around the geometric center of each face to create a certain angle. This ensures that when the facade is closed, all node positions are staggered.

In terms of geometric form, the unfolding of the skin is achieved based on the principles of tessellation geometry. From a mechanical perspective, this system belongs to a single-degree-of-freedom system, where each dynamic unit has a determined trajectory, and the movement state of the mechanism can be determined by a single parameter.
Differing from traditional distributed drives, this device explores a mechanical motion method known as single-axis driving. It utilizes the linear movement of driving points to propel the entire structure. This approach allows for the overall movement of the system to be achieved through the local movement of simple components, providing advantages such as a simple power mechanism and strong system robustness. In the single-axis driving mechanism, stationary points, driving points, and sliding axes are its main components. Each facade has its geometric center as a stationary point, and the corner point of a unit on one side serves as the driving point to slide along the outer frame, enabling the rotation and unfolding of 121 square panels. The sliders serving as driving points are constrained to the guide rails, which are hidden within the frame. Furthermore, the four sliders on the same facade are connected into a closed 'drive loop' through a steel cable and eight corner pulleys, making the facade units more stable under a centrally symmetrical force state.
The interactive device employs a single power source, driven by a small motor that powers the four faces of the central cube in the device, comprising a total of 484 discrete units. The motor shaft is fixed through a flange plate to a winding drum, and it drives a steel cable connected to a slider on the 'drive face' upper part. Another driving steel cable is connected to a slider on the vertical side of the 'drive face' and is fixed through a fixed hole in the winding drum by passing through a corner pulley. The two driving cables form a closed 'power loop'. Adjacent 'drive loops' share a slider, resulting in opposite rotation directions for adjacent faces. The unfolding and closing of the four facade skins are controlled by the clockwise and counterclockwise rotation of the motor shaft.


Before completing the full-scale version, a small-scale device was constructed as a preliminary step to validate the feasibility of the movable skin mechanism in terms of mechanical structure.
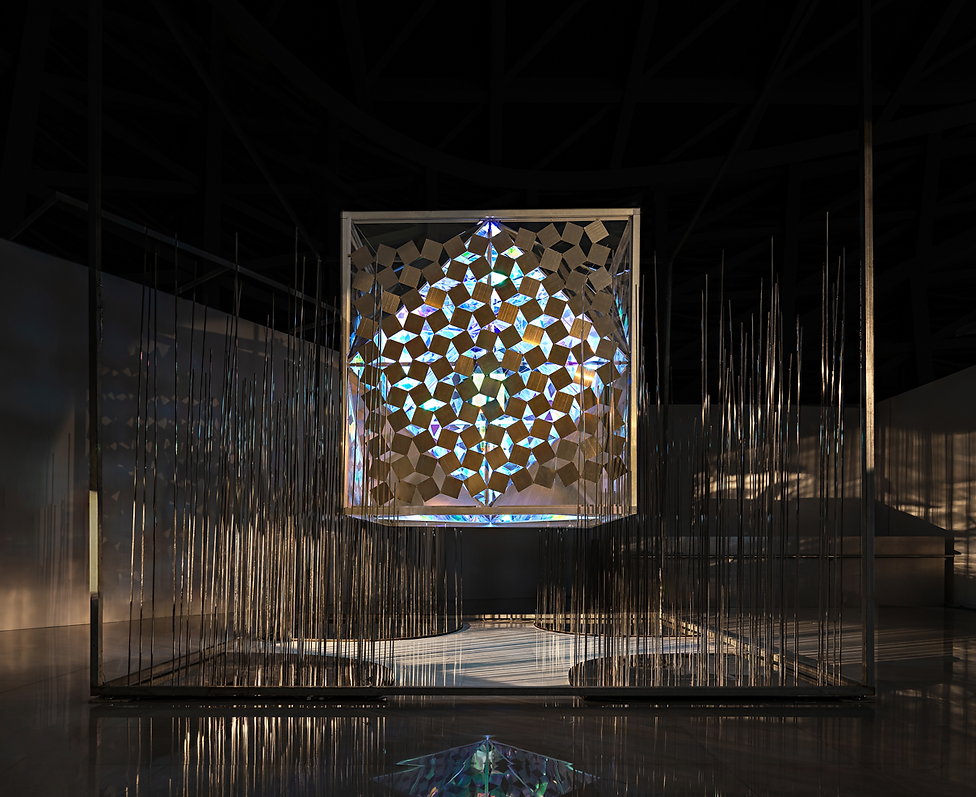

